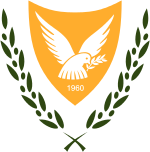
DCA
CYPRUS
AIC C 008/2008 - Effective 13 Nov 2008
ENGINE AND PROPELLER OVERHAUL PERIODS
1. INTRODUCTION
This AIC states the Cyprus Department of Civil Aviation requirement regarding piston engine and propeller overhaul periods for aircraft with a Cyprus Certificate of Airworthiness.
2. REQUIREMENT
It is required by Annex I of the European Commission Regulation (EC) No. 2042/2003, Part M.A. 302 of Part M that aircraft for which a certificate of airworthiness together with Airworthiness Review Certificate are in force be maintained in accordance with a DCA approved maintenance schedule.
The approved maintenance schedule requirements relating to overhaul of light aircraft Piston engines are defined as the engine manufactures´ recommended overhaul periods.
DCA policy in respect of extension of the calendar time to the recommended overhaul periods for piston engines used in light aircraft (private flights) are set out in Appendix 1 to this AIC.
Requirements for propeller type for which the manufacturer publishes no calendar overhaul period are described in paragraph 4 of this AIC.
The engine must have been operated in an aircraft registered in any EU member state for a period of at least 200 hours immediately prior to completion of the engine manufacturer´s overhaul period recommendation.
3. DEFINITIONS
Light aircraft piston engine: a piston engine installed in an aircraft, the Maximum Take Off Weight of which does not exceed 2730 kg or a piston engine of 400 hp (298 kW) or less.
Engine: an engine used or intended to be used for aircraft propulsion. It consists of at least those components and equipment necessary for the functioning and control, but excludes the propeller.
Public transport aircraft: those aircraft included in an Air Operators Certificate
Overhaul period: includes both operating time (hours) and calendar time (months/years)
4. PROPELLER OVERHAUL PERIODS WHERE THE MANUFACTURER PUBLISHES NO CALENDAR OVERHAUL PERIOD
Propellers shall be maintained in accordance with (a) of the appropriate following tables, unless the propeller manufacturer publishes no calendar overhaul period. In this case they shall be maintained in accordance with (b):
Table 1: Propellers fitted to Aircraft with MTOW of 5700 kg or above
(a) | Overhaul period: | Whichever occurs first of operating hours or calendar period as published by the propeller manufacturer unless varied by the DCA Approved Maintenance Programme. |
(b) | Overhaul period: | Operating hours as published by the propeller manufacturer or on condition where no life has been published, subject to (i) and (ii) below. |
(i) Hub/ blade inspection period: | Inspect at 3 years since new or overhaul or bare blade inspection below; repeat at 1-year intervals. |
(ii) Bare blade inspection period: | Not to exceed 6 years since new, overhaul or last bare blade inspection. |
Table 2: Propellers fitted to Aircraft with MTOW below 5700 kg
(a) | Overhaul period: | Whichever occurs first of operating hours or calendar period as published by the propeller manufacturer unless varied by the DCA Approved Maintenance Programme. |
(b) | Overhaul period: | Operating hours as published by the propeller manufacturer or on condition where no calendar life has been published subject to (i) and (ii) below. |
(i) Hub/ blade inspection period: | Inspect at 3 years since new or overhaul or Bare blade inspection below |
(ii) Bare blade inspection period: | Not to exceed 6 years since new, overhaul or last bare blade inspection. |
Hub/blade inspections and bare blade inspections are defined in Appendix 2 of this AIC.
This AIC cancels the previous AIC C012/06 dated 17 May 2006
APPENDIX 1 TO AIC C012/2006
LIGHT AIRCRAFT PISTON ENGINE MAINTENANCE REQUIREMENTS FOR OPERATION BEYOND MANUFACTURERS’ RECOMENDED OVERHAUL PERIODS
1. This appendix gives guidance on the procedures that are necessary for a light aircraft piston engine to be accepted as being in a condition that will allow operation beyond the recommended overhaul period (Calendar Time), under the terms of this AIC.
2. The inspections and tests that are necessary to assess the condition of an engine in compliance with this AIC are detailed in the following paragraphs. These must be carried out at 50 hour or six month intervals by appropriately qualified and approved mechanics or maintenance organisations.
3. Inspections and Maintenance
A number of items included in the normal scheduled maintenance of an engine may be repeated to determine the condition of an engine at the end of its normal overhaul period, and additional inspections may also be specified.
3.1 External Condition. The engine should be examined externally for obvious defects such as a cracked crankcase, excessive play in the propeller shaft, overheating and corrosion, which would make it unacceptable for further use.
3.2 Internal Condition. Significant information concerning the internal condition of an engine may be obtained from an examination of the oil filters and magnetic plugs, for metal particle contamination. A boroscope check shall also be carried out to establish the cylinder, piston, valve and valve seat condition. These checks may be sufficient to show that serious wear or breakdown has taken place and that the engine is unacceptable for further service.
3.3 Oil Consumption. Since the oil consumption of an engine may have increased towards the end of its normal overhaul period, an accurate check of the consumption over the last 10 flying hours would show whether it is likely to exceed the maximum recommended by the constructor, if the overhaul period were to be extended.
3.4 Compression Check. Piston ring or cylinder wear, or poor valve sealing could, in addition to increasing oil consumption, result in a significant loss of power. A cylinder compression check is a method of determining, without major disassembly, the standard of sealing provided by the valves and piston rings.
3.4.1 On engines with a small number of cylinders, a simple compression check may becarried out by rotating the engine by hand and noting the resistance to rotational as each cylinder passes through its compression stroke. The check should normally be made shortly after running the engine while a film of oil remains on the rubbing surfaces, to assist sealing and prevent scoring the working parts. If this is not possible, the constructor may recommend that oil is introduced into each cylinder and the engine turned through a number of revolutions before making the test. This method may be used to determine serious loss of compression on a single cylinder or the difference between the compressions of individual cylinders, but may not accurately show a similar partial loss of compression on all the cylinders of an engine. An alternative method, which will give a more accurate result, is to fit a pressure gauge (reading up to 1400 kPa (200 lbf/in2)) in place of one sparking plug in each cylinder in turn and note the reading as the piston passes through top dead centre (TDC) on the compression stroke.
3.4.2 Another method of carrying out a direct compression test is by the use of a proprietary type of compression tester equipped with a means of recording cylinder pressure on a graph card. One set of plugs should be removed immediately after an engine run, and the compression tester fitted to each cylinder in turn while rotating the engine by means of the starter motor. The effectiveness of combustion charge sealing can be judged by assessment of the graph records obtained.
3.4.3 A further method of checking engine compression is the differential pressure test. In this test a regulated air supply (normally 560kPa (80 lbf/in2)) is applied to each cylindering turn and a pressure gauge used to record the actual air pressure in the cylinder. Since some leakage will normally occur, cylinder pressure will usually be less than supply pressure and the difference will be an indication of the condition of the piston rings and valves. By listening for escaping air at the carburetor intake, exhaust and crankcase breather, a defective component may be located. As with the previous tests, it is usually recommended that the differential pressure test is carried out as soon as possible after running the engine.
4. Power Output of Aeroplane Engines (to be carried out when the engineer suspects (or pilot reports) power loss, or if requested by the DCA Airworthiness Section)
The power developed by an aeroplane engine after initial installation is established in the form of a reference engine speed, which is recorded in the appropriate log book so that a comparison can be made during subsequent power checks. The reference engine speed is the observed engine speed obtained using specified power settings and conditions, corrected, by means of graphs supplied by the engine constructor (or those contained in the UK CAA Civil Aircraft Airworthiness Information and Procedures - CAP 562 Leaflet 7-5 Piston Engine Overhaul – Correcting Engine Test Results), to the figure which would be obtained at standard sea-level atmospheric temperature and pressure; changes in humidity do not produce large changes of power and are ignored for the purpose of establishing a reference engine speed or subsequently checking engine power. Power checks should be corrected in the same way.
4.1 Power Checks. The majority of light aeroplane piston engines are air-cooled and rely on an adequate flow of air for proper cooling of the cylinders. This condition can only be obtained during flight, and ground runs should, therefore, be as brief as possible. Cooling can be assisted by facing the aircraft into wind, but high wind conditions must be avoided when making power checks, as they will seriously affect the results obtained. Before running the engine at high power the normal operating temperatures should be obtained (not the minimum temperatures specified for operation) and during the test careful watch should be kept on oil and cylinder temperatures to prevent the appropriate limitations being exceeded.
4.1.1 Normally-aspirated engines are tested at full throttle and, where a controllable-pitch propeller is fitted, with fully fine pitch selected. The changes in barometric pressure affecting engine power are considered to be balanced by changes in propeller load, so that only a temperature correction is necessary. This correction factor may be
obtained from a graph supplied by the engine constructor or, if this is not available, from the graph shown in the UK CAA Civil Aircraft Airworthiness Information and Procedures (CAP 562) Leaflet 7-5 Piston Engine Overhaul – Correcting Engine Test Results (Figure 1). The observed full throttle speed multiplied by the correction factor will give the corrected speed.
4.1.2 Although normally-aspirated engines are often fitted with variable-pitch propellers, the engine speed obtained at full throttle is usually less than the governed speed and the propeller remains in fully fine pitch. With supercharged engines, however, the propeller is usually governed to a constant speed at high power settings and small changes in power will not affect engine speed. The power of a supercharged engine is, therefore, checked by establishing a reference speed at prescribed power settings.
- Since a supercharged engine is run at a specified manifold pressure regardless of the atmospheric pressure, corrections must be made for both temperature and pressure variations from the standard atmosphere.
- The procedure is to run the engine until normal operating temperatures are obtained, open up to maximum take-off manifold pressure, decrease power until a fall in engine speed occurs (denoting that the propeller blades are on their fine pitch tops), then throttle back to the manifold pressure prescribed by the constructor and observe the engine speed obtained.
- The correction factor to be applied to the observed engine speed of a supercharged engine may be obtained from graphs supplied by the engine constructor.
4.1.3 Although the engine speed obtained during a check of engine power is corrected as necessary for atmospheric temperature and pressure, no correction is made for humidity, ambient wind conditions or instrument errors and, consequently, the corrected engine speed is seldom exactly equal to the reference speed even if engine condition is unchanged. However engine power may usually be considered satisfactory if the corrected speed obtained during a power check is within 3% of the reference speed.
4.1.4 If it is not possible to assess power deterioration by means of a power check (e.g. due to fitting a different propeller or insufficient data), an airworthiness flight test should be carried out.
5. Power Output of Helicopter Engines
The power developed by the engine of a single-engine helicopter is considered to be adequately checked during normal operations; any loss of power should be readily apparent. It is thus not considered necessary to check the power output of a helicopter engine separately specifically for the purpose of complying with this AIC.
6. Power Loss
If the power check (paragraph 4) or normal engine operation reveal an unacceptable loss of power or rough running, it may be possible to rectify this by carrying out certain normal servicing operations or by replacement of components or equipment. The replacement of sparking plugs, resetting of tappets or magneto contact breaker points, or other adjustments to the ignition or carburetion systems, are all operations that may result in smoother running and improve engine power.
7. Servicing
If the engine proves to be suitable for further service, a number of servicing operations will normally be due, in accordance with the approved Maintenance Schedule. Unless carried out previously (paragraph 6) these operations should be completed before the engine is returned to service.
8. The above checks made and any rectification or servicing work shall be carried out in accordance with the manufacturer’s instructions. A comprehensive record of the inspection and work done on the engine in accordance with this Appendix shall be retained and an entry, making a reference to this record and to this AIC, shall be inserted in the Engine Log Book.
APPENDIX 2 TO AIC C012/2006
1. Hub/blade inspection.
- Dismantling of the propeller sufficiently to gain access to the blade root bearing assemblies.
- Thorough cleaning of the blade root assemblies in accordance with the manufacturer’s instructions.
- Examination for pitting, fretting, corrosion, cracking and other damage of the hub, bearings, blade roots, and housing, together with replacement of any disturbed seals. All of the blade surfaces shall be examined for damage, delamination (where applicable), and the presence of corrosion, removing the paint finish as necessary. In cases where de-icer boots or overshoes are installed on the blades, a detailed examination for corrosion around their edges shall be carried out, and, if any evidence is found, the boots/overshoes shall be removed to permit a full inspection of the masked areas. Any corrosion shall be removed and the blades reprotected. In cases where de-icer boots/overshoes are removed, replacement parts shall be installed using the facilities prescribed and under conditions and procedures specified, in the relevant manufacturer’s Overhaul Manual.
- Non-Destructive Inspection of the hub and blade roots shall be carried out in accordance with the manufacturer’s instructions except where it can be verified that Non-Destructive Inspection of the hub and blade roots has been carried out in accordance with the manufacturer’s instructions within the last 4 years.
- Checking the track of the propeller after refitting, then functioning throughout its operational range by means of an engine run to verify correct performance, and to establish that any vibration is within acceptance limits, in accordance with the manufacturer’s instructions.
2. Bare blade inspection
In addition to the hub/blade inspection described above:
- Removal of all de-icing boots or overshoes and fairings.
- Removal of all paint and erosion protection.
- Removal of all blade root bushings and plugs.
- Inspection of the complete blade surface for the presence of corrosion. Any corrosion shall be removed and the blades re-protected and prepared for the reinstallation of the blade fittings.
- All Non-Destructive Inspection required for overhaul of the propeller shall be carried out in accordance with the manufacturer’s instructions.
- Full dimensional inspection of all blades.
3. The above inspections and re-work shall be carried out in accordance with the manufacturer’s instructions. A comprehensive record of the inspection and work done on the propeller in accordance with this Appendix shall be retained and an entry, making a reference to this record and to this AIC, shall be inserted in the Propeller Log Book.